Handling, protection & safe storage of roofing materials
The protective properties of both zinc and paint coatings may suffer significant deterioration when exposed to prolonged wet conditions without air. In such circumstances, the zinc surface becomes vulnerable to corrosion during extended storage if appropriate precautions are not taken.
Rainwater or water vapor (condensation) can seep between tightly packed profile sheets or coil laps due to capillary action. Without adequate air circulation, moisture cannot evaporate, leading to conditions conducive to wet storage corrosion, often referred to as "white rust" or "wet-storage stain" on galvanized sheeting. For pre-painted materials, such conditions may result in paint discoloration and, in severe cases, wet storage corrosion similar to that seen on galvanized sheeting.
Wet storage corrosion can quickly occur after nested packs, coils, or sheets are exposed to damp conditions, potentially impacting the expected maintenance-free lifespan of the material unless addressed promptly. To prevent wet storage corrosion, it's essential to ensure that nested packs, coils, or sheets remain exposed to continuous, freely circulating air.
Failure to adhere to these precautions may leave sheets vulnerable to wet storage corrosion, especially when stored under adverse wet conditions.
Material inspection upon receipt:
Upon receiving coils and bundles of galvanized or color-coated profile sheets from the manufacturer, it's crucial to carefully inspect their condition.
If galvanized or color-coated coils and profile sheets need to be stored for more than fourteen days, efforts should be made to keep them dry during transport and covered storage.
If moisture is detected in bundles or packs upon delivery, a complaint should be lodged with the supplier.
These packs should be promptly opened, and the individual sheets separated and dried before storage.
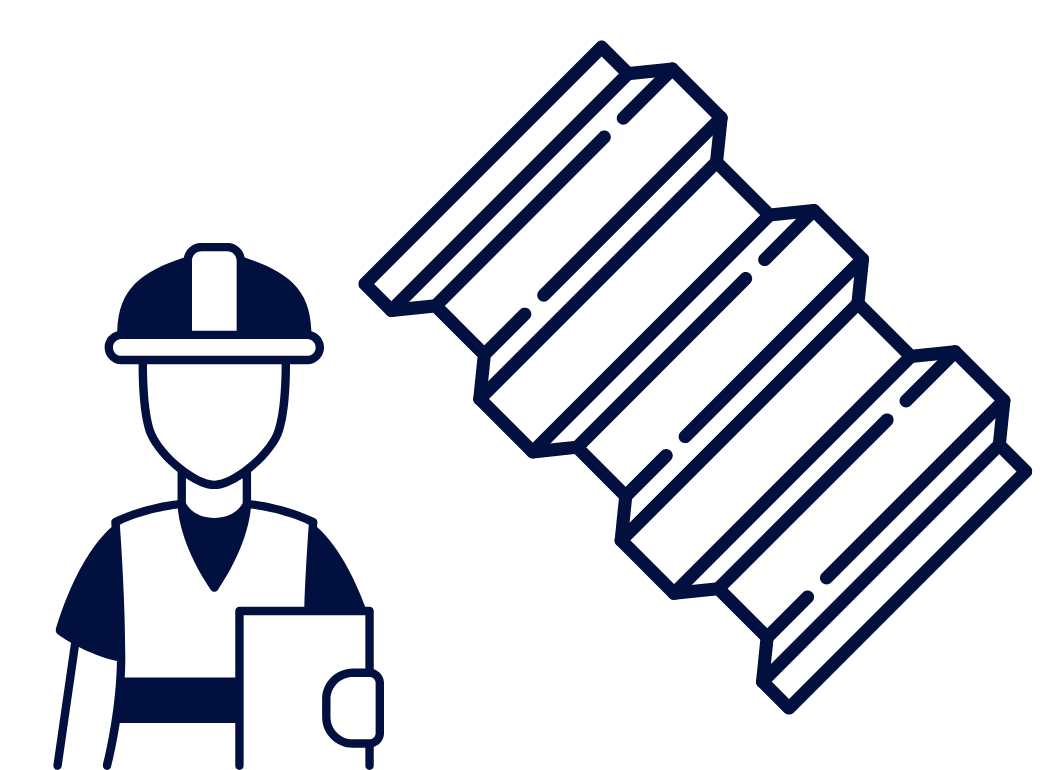
Safe storage:
To prevent unnecessary damage to galvanized and color-coated coils or profile sheets, special precautions should be taken to avoid moisture contamination.
If galvanized and color-coated coils or profile sheets are not immediately needed, coils or packs should be stored above ground level at the site under properly designed cover, shielded from wind-driven rain.
Plastic tarps that fully enclose packs of sheets or coils should be avoided, as sudden drops in temperature can lead to condensation or water formation, which can be drawn in between nested sheets due to capillary action.
Ideally, deliveries of galvanized or color-coated sheets to the construction site should be timed so that the storage period does not exceed two weeks before installation.
Regular inspection of the storage site is strongly recommended to prevent moisture penetration into the stock.
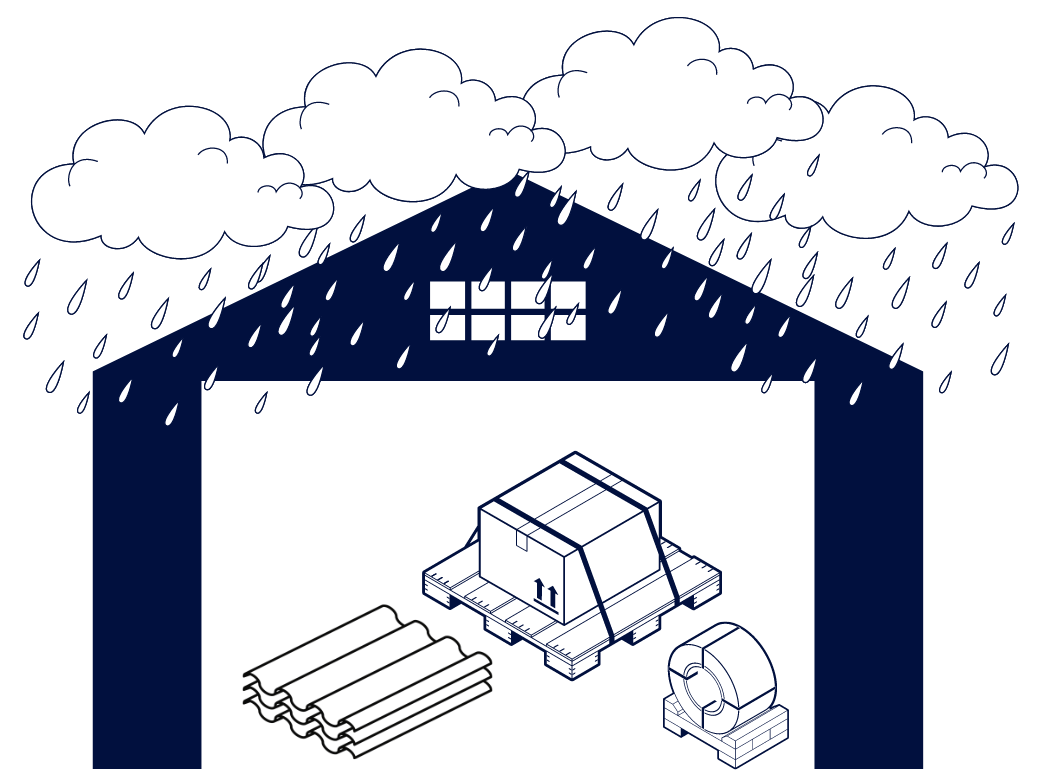
Visible Effect | Cause | Remedial Action |
---|---|---|
Phase 1: Light white discoloration - thin, powdery white deposit. | Moisture trapped between sheets or components during transport or storage, or condensation due to poor ventilation. | No action needed. The zinc's protective qualities remain unaffected by a superficial white deposit. These deposits will gradually turn into a protective zinc carbonate layer. Not suitable for post-painting without removing any loosely adhering deposits. |
Phase 2: Heavy white discoloration - thick, crusty deposits. | Extended storage in poor conditions or insufficient protection during transport, leading to significant water ingress between closely packed sheets or components. | Before painting, remove all loosely adhering deposits using a stiff bristle brush (avoid wire brushes). Check the zinc coating thickness with a magnetic gauge. If the thickness meets specifications and the sheet or component will be used in dry or openly exposed conditions, no further action is needed. |
Phase 3: Black staining and white discoloration with powdery deposits. | Initial stages of superficial zinc corrosion, usually from the formation of complex surface corrosion products. Black staining does not necessarily mean the zinc coating is compromised. | Verify the zinc coating thickness using a magnetic thickness gauge. If unsure, consult a paint expert recommended by NJR Steel staff before painting, as stains can be complex. |
Phase 4: Red rust. | Corrosion of the steel substrate where the zinc coating has completely deteriorated. This should not be mistaken for superficial staining. | Generally, sheets or components with this defect should be discarded and not used. |
GET PRICING FROM YOUR
NEAREST NJR STEEL BRANCH
We have 21 branches across 7 provinces that are ready and willing to help you. Talk to us today to get pricing or just advice for your next project.